Collaborative robotics like person-to-goods or 'pick assist' AMRs are intelligently designed to work with people, not replace them. Adoption of AMRs for automated order fulfillment is turning this challenge into a competitive advantage.
The Human + Robot Workforce: How Collaborative Robotics Are Solving the Labor Crisis
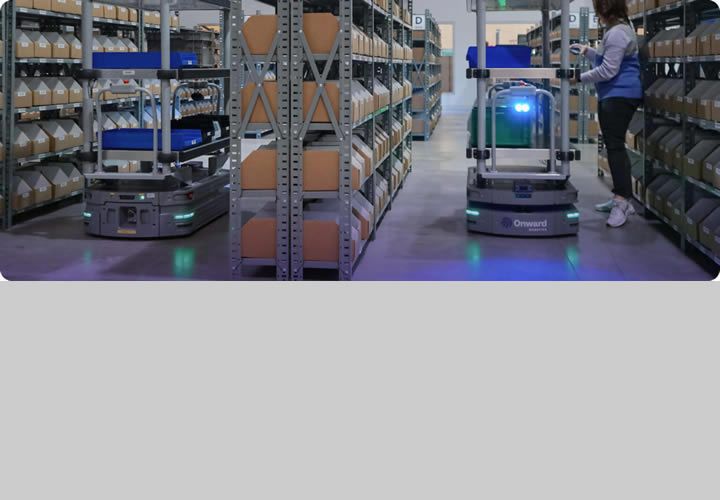
Article from | Onward Robotics
Across retail, e-commerce, third-party logistics, and warehousing, labor shortages continue to challenge the efficiency and scalability of fulfillment operations. Rising order volumes, high employee turnover, and increasing customer expectations have exposed the limitations of relying solely on a human workforce. But there’s good news: collaborative robotics like person-to-goods or “pick assist” AMRs are intelligently designed to work with people, not replace them. Adoption of AMRs for automated order fulfillment is turning this challenge into a competitive advantage.
At Onward Robotics, we believe the future of fulfillment lies in a human + robot workforce, where each contributes what they do best.
The Labor Crisis Is Real—and Growing
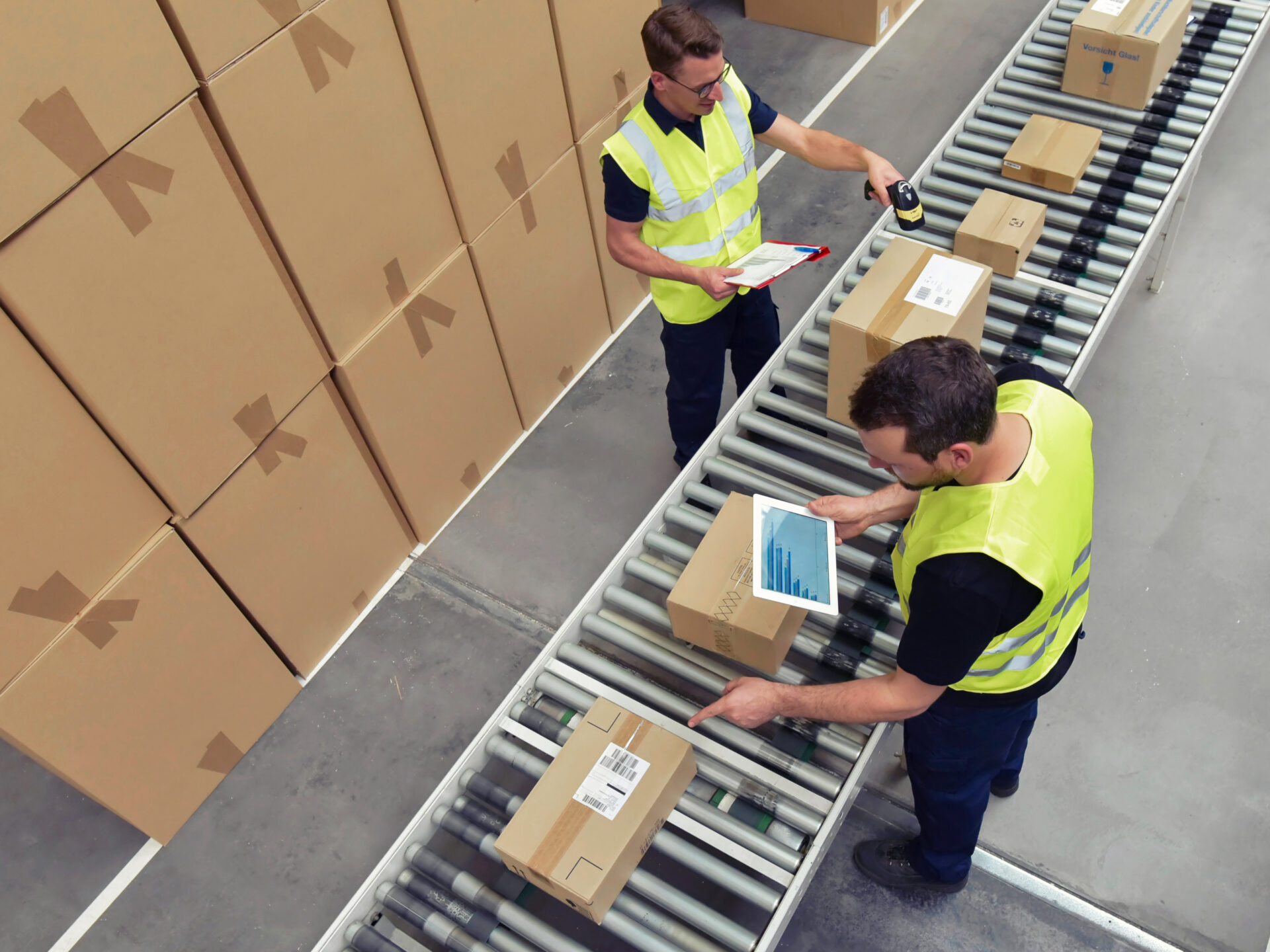
Warehouses and distribution centers across the country are struggling to recruit and retain workers. Labor-intensive roles, seasonal spikes, and physically demanding tasks make staffing a constant challenge. And as e-commerce continues to grow, that gap between demand and workforce capacity only widens. In fact, the U.S. warehousing and storage industry is projected to have over 400,000 unfilled jobs by 2028, according to the U.S. Bureau of Labor Statistics.
Traditional automation approaches—like fixed conveyors or goods-to-person systems—have helped, but they come with long installation times, high infrastructure costs, and limited flexibility. In a dynamic environment, speed and adaptability are essential.
Enter Collaborative Robotics: Smarter, Faster, More Human
Pick Assist Autonomous Mobile Robots (AMRs) offer a fundamentally different approach to warehouse automation. Rather than replacing human labor, these systems are designed to work alongside people—enhancing efficiency, reducing physical strain, and improving overall throughput in the order fulfillment process.
By intelligently coordinating the flow of goods and tasks between workers and robots, person-to-goods AMRs create a more balanced and productive environment. Workers stay focused on value-added tasks like picking, while AMRs handle repetitive and time-consuming transport tasks.
These systems are typically infrastructure-free, making them fast to deploy, easy to scale, and a clear favorite option for brownfield sites or greenfields that aim to remain agile in evolving markets. Infrastructure-free flexibility allows warehouses to adapt quickly to labor fluctuations, seasonal demand spikes, or shifting operational priorities—without costly or time-intensive reconfigurations.
Benefits of the Human + Robot Workforce:
Boosted Throughput
Robots handle the heavy lifting—literally and logistically—allowing human workers to focus on picking, packing, and quality control.
Reduced Turnover
When physical strain is reduced and workflows are more intuitive, employees are more likely to stay.
Faster Ramp-Up During Peak
Automation scales up quickly to handle increased volume, without the delays and costs of seasonal hiring.
Improved Worker Satisfaction
When workers are supported by intuitive, helpful automation, they’re more productive—and more satisfied.
Real-Time Insights
Business intelligence software monitors real-time conditions and adjusts task assignments to ensure maximum efficiency and uptime.
Robots Aren’t Replacing People—They’re Empowering Them
Collaborative Robots Reduce Strain, Improve Retention, and Help Workers Focus on High-Value Fulfillment Tasks
The fear that automation will eliminate jobs misses the bigger picture. In modern fulfillment and logistics operations, collaborative robots—especially person-to-goods or “pick assist” AMRs—are not replacing workers but enabling them to do more with less strain. These systems are designed to extend human capability, not compete with it.
By minimizing the walking and repetitive transport tasks that typically consume a large portion of a warehouse worker’s day, collaborative robots allow employees to focus on higher-value responsibilities such as picking, packing, or quality control. This not only improves operational efficiency but also makes the work itself less physically taxing and more rewarding.
When employees are freed from exhausting or monotonous tasks, they’re more likely to stay engaged, productive, and satisfied. In an industry known for high turnover, that matters. Improved job satisfaction directly contributes to better retention—reducing the costs and time associated with recruiting and training new staff.
Ultimately, the synergy between people and collaborative robots creates a stronger, more resilient workforce. Humans bring adaptability, judgment, and fine motor skills. Robots bring consistency, speed, and strength. Together, they can meet today’s fulfillment demands and tomorrow’s growth opportunities—smarter, faster, and more sustainably.
Let’s Move Onward, Together
How Meet Me® Automation Supports a Stronger Warehouse Workforce
At Onward Robotics, we’ve engineered our Lumabot person-to-goods AMRs and intelligent Pyxis software to directly support fulfillment teams facing labor shortages and rising demand. By combining automation with human strengths, we help operations do more with the workforce they have—without sacrificing speed, accuracy, or employee well-being.
Our collaborative approach delivers measurable impact through:
- Human + Robot Coordination: Real-time task orchestration ensures people and AMRs work together efficiently
- Reduced Physical Strain: Less walking and repetitive movement means safer, more sustainable jobs
- Increased Throughput: Automating non-value-added tasks frees up workers to focus on critical operations
- Higher Employee Satisfaction: Empowered workers are more engaged, more productive—and more likely to stay
- Fast, Flexible Deployment: Infrastructure-free setup enables rapid scaling, even during peak season
The content & opinions in this article are the author’s and do not necessarily represent the views of RoboticsTomorrow
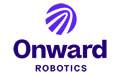
Onward Robotics
Onward Robotics delivers innovative automation technology that coordinates humans and robots as a cohesive system to revolutionize fulfillment. Our Meet Me® solution combines proprietary software with person-to-goods mobile robots to increase efficiency in warehousing, distribution, and e-commerce operations. Onward Robotics provides the boost in productivity, flexibility, and speed that companies need to remain competitive and grow.
Other Articles
Order Picking Methods: Finding the Right Strategy for You
Meet, Find, Follow: Comparing 3 Ways to Automate With Order Fulfillment Robots
More about Onward Robotics
Comments (0)
This post does not have any comments. Be the first to leave a comment below.
Featured Product
