Intel's 3-D Printed Robot "Jimmy"
TravelByDrone
Blocky: A Graphic Programming Environment for ROS
iCEstick $25 FPGA Evaluation Kit
Paraplegic in robotic suit kicks off World Cup
Response by Ray Kurzweil to the announcement of chatbot passing the Turing test
Tessel: A Microcontroller That Runs JavaScript
Open-source 3D Printed Life-size Robot
Algorithm that harnesses data from a new sensor could make autonomous robots more nimble.
Leap Motion V2 Tracking
VoCore: A Coin-sized Linux Computer With Wifi
Printed Hand With An Opposable Thumb
DARwIn-mini
3D Video Capture With Three Kinects
Parrot Bebop
Records 1351 to 1365 of 1630
First | Previous | Next | Last
Featured Product
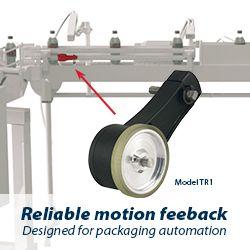