SW Automation presents a world first at automatica with its mobile robot cell
New modular and connectable Mobile i-Cell from SW
Tettnang, May 06, 2025: Schwäbische Werkzeugmaschinen GmbH (SW) is presenting a new solution for modular automation at automatica 2025 in Hall A5, Stand 321: the Mobile i-Cell robot cell, which is a scalable unit that flexibly connects assembly, logistics, and machining stations. It supports manufacturing companies in the automated and efficient machining of a wide variety of components and order volumes—without rigid interlinking or complex integration.
Schwäbische Werkzeugmaschinen GmbH (SW) and its subsidiary SW Automation GmbH will be presenting the Mobile i-Cell, a mobile robot cell, for the first time from June 24 to 27. It takes over automated processes such as handling workpieces and operating machining, washing, or assembly stations, thereby replacing manual processes in production. "As a mobile unit for automated machining, the Mobile i-Cell opens up new possibilities - from small-scale to easily expandable large-scale automation," says Roman Wolf, team leader for control technology development at SW Automation. With its combination of high productivity, modular design, flexible application options, and end-to-end connectivity, the self-sufficient Mobile i-Cell fits seamlessly into modern manufacturing environments - especially where product diversity and dynamic production requirements are commonplace.
Flexible positioning, targeted automation
The i-Cell is mounted on a mobile carrier system and can be moved through the production environment using a driverless transport system (Mobile i-Wagon). The cell docks at the desired station, be it machining, washing, assembly, or a DMC laser station. An integrated robot with a gripping system takes the raw material from upstream storage stations, known as Mobile i-Storages, loads the machining station, and returns the workpieces after completing the process. The Mobile i-Storages are also automatically movable by the Mobile i-Wagon, and the workpieces are fed and removed independently of the cell. "The flexible docking eliminates the need for complex and rigid coupling of the processing stations with the robot cells - and our customers gain efficiency and design freedom," explains Roman Wolf. This saves space, increases machine availability, and makes production processes more adaptable. The system automatically recognizes the respective station type and adapts processes - without time-consuming manual changeovers or recommissioning.
The Mobile i-Cell presented at automatica is designed for payloads of up to 120 kg. The cell can be flexibly networked with SW machines as well as with systems from other manufacturers. Power supply and control are handled directly by the respective station or via SW's own automation platform, which orchestrates robots, transport systems, and order data.
Another advantage is that the cell only docks at a station temporarily, keeping the station freely accessible at all other times - for cleaning, maintenance or similar tasks. This keeps the system highly available and easy to integrate.
Modular production concept for greater flexibility and scalability
The strengths of the concept lie in its modularity and mobility. Companies can start with just a few modules and expand the system step by step as required - a clear advantage over fixed production lines. "This means that investments remain predictable and can be adapted to changing requirements," emphasizes Wolf. The Mobile i-Cell demonstrates its advantages particularly when component types and quantities change frequently, such as in the automotive industry with engine blocks, oil pans, or bushings. By using several cells in parallel the system runs consistently at high capacity, even with short cycle times of less than 10 minutes. Companies also benefit from the modular concept: they can start with just a few units and expand the system flexibly as needed.
The Mobile i-Cell is patent-pending and will be demonstrated live for the first time at automatica in conjunction with an AGV. An interactive display will show the possible applications and flexible docking at different stations. The robotics and AMRs used are being provided by system partner KUKA, the exhibitor at the neighboring booth. With the Mobile i-Cell, SW lives up to its claim to continuously optimize production - piece by piece, "best per part". The solution is part of the company's Smart Manufacturing Solutions, which enable modern and adaptable manufacturing concepts for specific customer requirements. SW will be showing what they can look like at its booth in a 3D miniature model.
SW at automatica 2025 from June 24-27, Hall A5, Booth 321
Featured Product
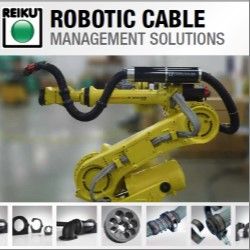
REIKU's Cable Saver™ - The Most Versatile Modular Robotic Cable Management Solution
REIKU's Cable Saver™ Solution eliminates downtime, loss of revenue, expensive cable and hose replacement costs, maintenance labor costs. It's available in three sizes 36, 52 and 70 mm.
All of the robots cables and hoses are protected when routed through the Cable Saver™ corrugated tubing.The Cable Saver™ uses a spring retraction system housed inside the Energy Tube™ to keep this service loop out of harms way in safe location at the rear of the Robot when not required. The Cable Saver™ is a COMPLETE solution for any make or model of robot. It installs quickly-on either side of the robot and has been tested to resist over 15 million repetitive cycles.
REIKU is committed to providing the most modular, effective options for ensuring your robotic components operate without downtime due to cable management.
www.CableSaver.com